導入例をご紹介します
【これまでの対応実績】
- 工場内等の沈殿ピット
- タンク内清掃
- サイロ内クリーニング、回収
- 堆積スケール
- 炉内清掃
- 側溝清掃
- 工場内の堆積物(ダスト、グリス、油泥、スラッジ)の回収
- 油等の河川、道路への流出対応
- 各種高圧洗浄(配管内、タンク内、外壁等)
工場の稼働過程で出るクズを吸い取る
(定期メンテナンス)
コストダウン効率化トラブル回避保全
設備周辺に落ちてたまるクズを定期的に吸引し、生産の流れをスムーズにします。
ピット内の汚泥を吸い取る
(定期メンテナンス)
コストダウン効率化トラブル回避保全
固まりやすい、ピット内の汚泥を定期的なメンテナンスします。
工場床のベトベト油を吸い取る
コストダウン効率化トラブル回避保全コンプライアンス遵守
ベタベタになって落ちにくい工場の油を吸い取る作業です。
サイロ内に固着した堆積物を吸い取る
(人力から機械へ)
コストダウン効率化トラブル回避保全
サイロの能力を常に保つため、サイロ内にたまって固着した堆積物を吸い取ります。
地下にあるピットや遠方の物を吸い取る
(人の手の届かない場所)
コストダウン効率化トラブル回避保全
水路、地下のピットなど普段見えない場所をキレイにします。
どうしたらよいかわからないものを処理する
トラブル回避保全コンプライアンス遵守
中身が何かわからないもの、処分に困っているものの処分をサポートし、適切な方法をご提案致します。
吸引作業後に洗浄する(高圧洗浄)
スーパージェットクリーン=超超高圧洗浄機SZC工法
吸引作業後に高圧洗浄することで、より美しく仕上がります。汚れがなくなった分、貯蓄タンクなどの容量増加にもつながります。
水処理・汚泥処理
効率化トラブル回避保全
排水の処理がうまくいかない、汚泥の処理量が多く産廃費が高額といった問題点があればご相談下さい。専門のスタッフが代替案をご提案致します。
処理・設備トラブル対応
コストダウン効率化トラブル回避保全
排水処理設備が止まった、工事現場から汚水が出てきた、タンクから油が流出したなどトラブル対応致します。まずはご連絡下さい。
吸引作業の省人化(人間から、重機が吸引する時代へ)
効率化トラブル回避保全
ピット内の通気性の悪さ、熱中症の危険リスク、ホースの暴れによる接触リスクなどの3Kの作業環境を作業方法の進化で環境改善を図ります。また、新型アタッチメントの開発で、特許取得を目指しています。
工場の稼働過程で出るクズを吸い取る(定期メンテナンス)
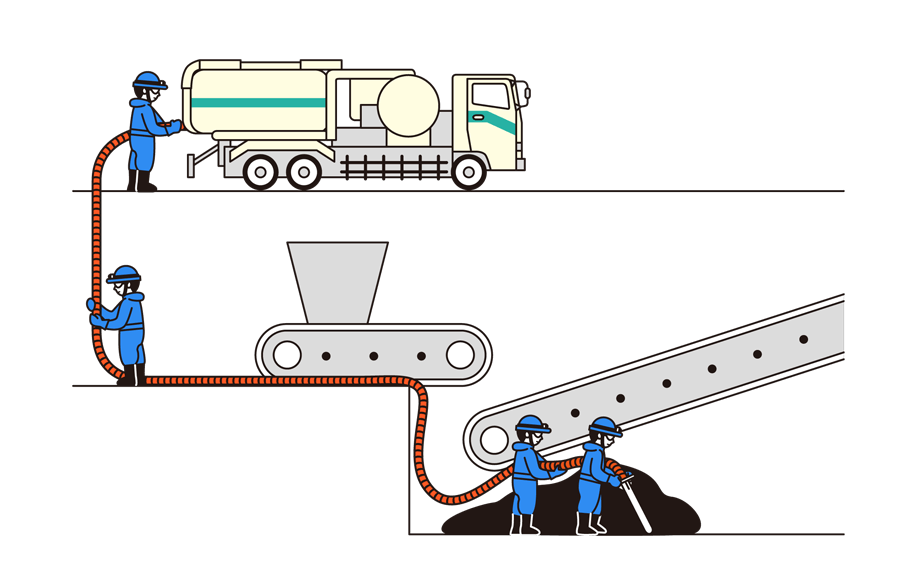
設備周辺に落ちてたまるクズは、放置するとベルトコンベヤーなどの機械が動かなくなり、生産がストップしてしまいます。
ピット内の汚泥を吸い取る(定期メンテナンス)
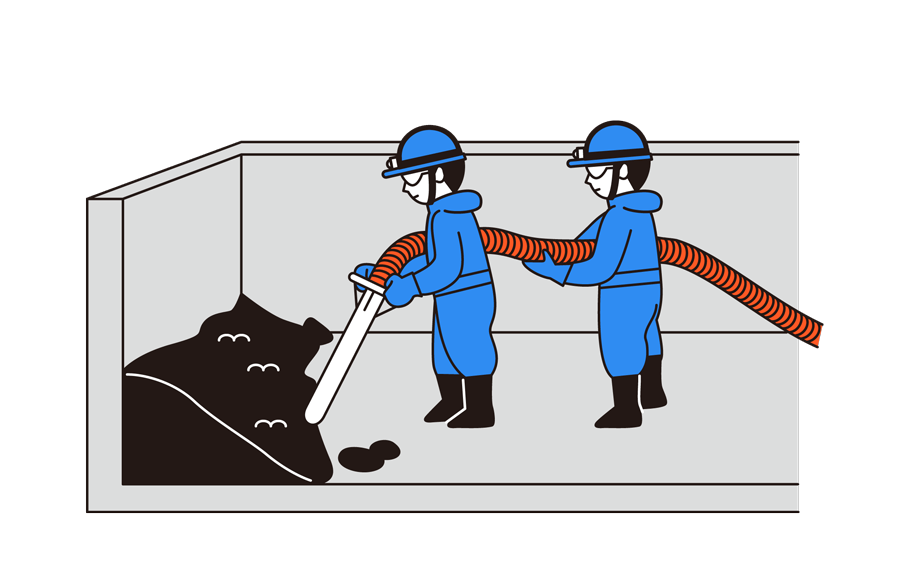
ピット内の汚泥は固まりやすく、放置するほど掃除が大変になるため、定期的なメンテナンスが必要不可欠です。汚泥は重く人力での清掃はかなりの重労働となります。
工場床のベトベト油を吸い取る
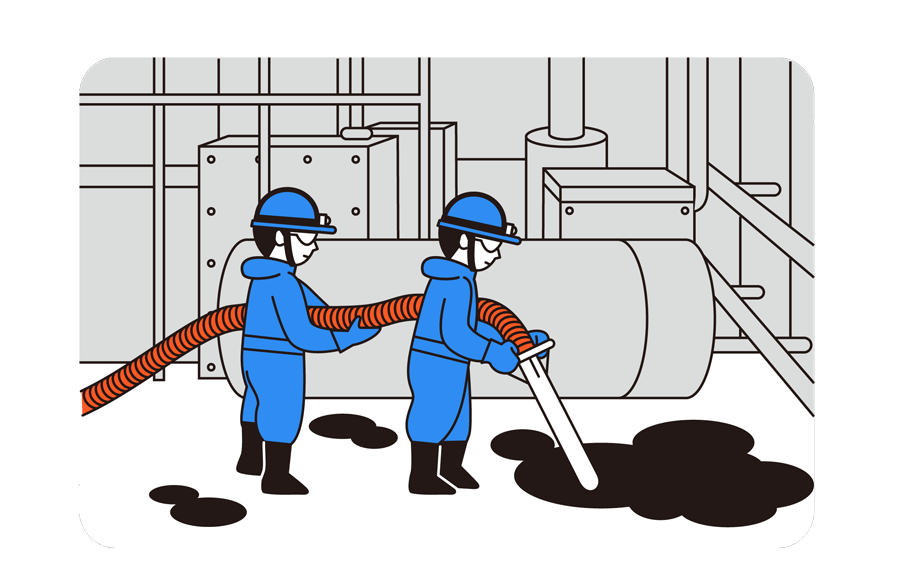
工場の油を吸い取る作業です。摺動部のグリス、油圧設備のオイル等のもれが発生した場合、放置していると衛生環境に悪いばかりでなく、火災などの原因になり危険なため、消防署から指摘されることも多いようです。消防の審査が入る前に清掃することもあります。
サイロ内に固着した堆積物を吸い取る(人力から機械へ)
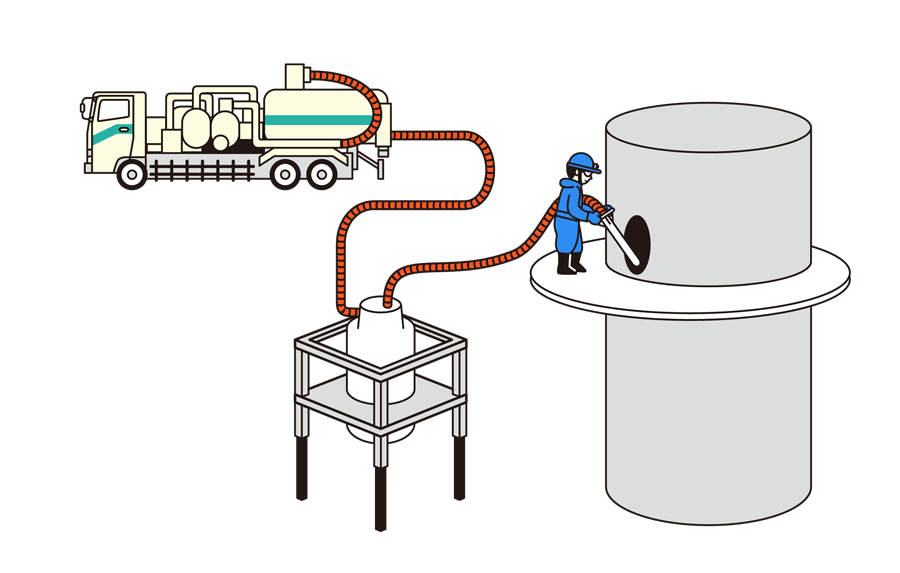
サイロは原料の固着により投入できる量の減少や、詰まり、固着物劣化による品質低下を発生させる場合があり、定期的な清掃を行い、サイロ内を清潔に保つ必要があります。
手作業での清掃は時間がかかり、内部の縁などにカスがたまりやすい状況でした。
回収した原料はフレコンバック等に積み替えることもでき再利用できます。
水路の汚泥やガソリンなどを吸い取る(人の手の届かない場所)
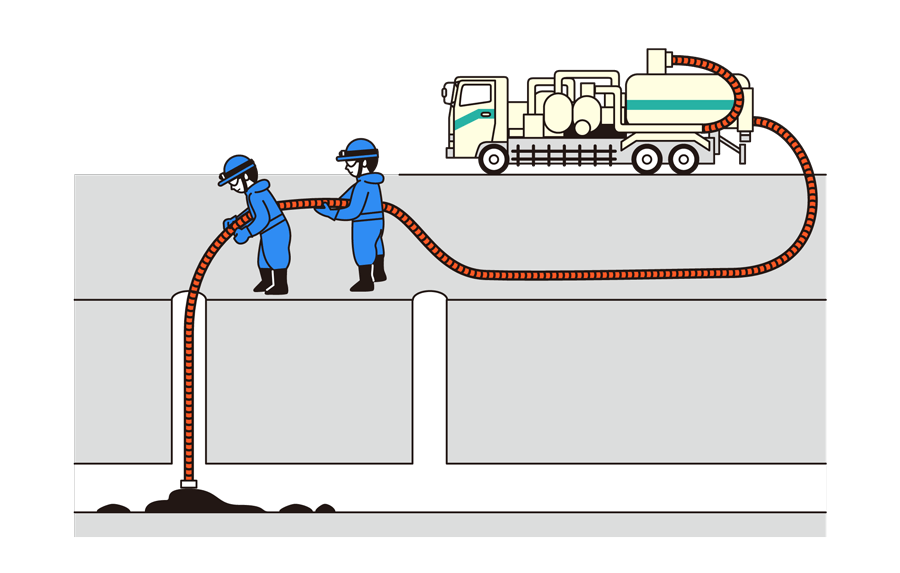
水路、地下のピットなど普段見えない場所には、人が立ち入るのが大変です。
どうしたらよいかわからないものを処理する
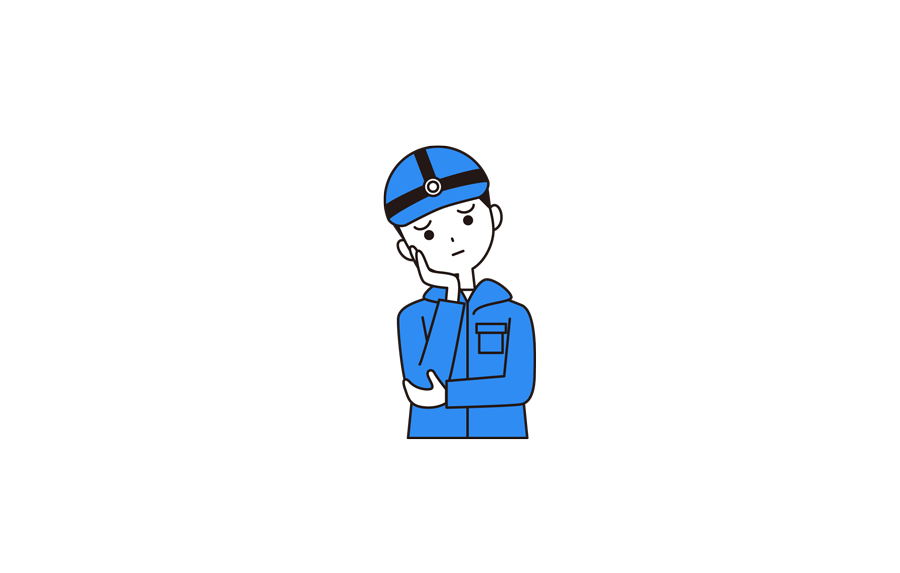
中身が何かわからない、どこに相談したら処理できるのかわからない、などの困ったものを処分します。
吸引作業後に洗浄する(高圧洗浄)
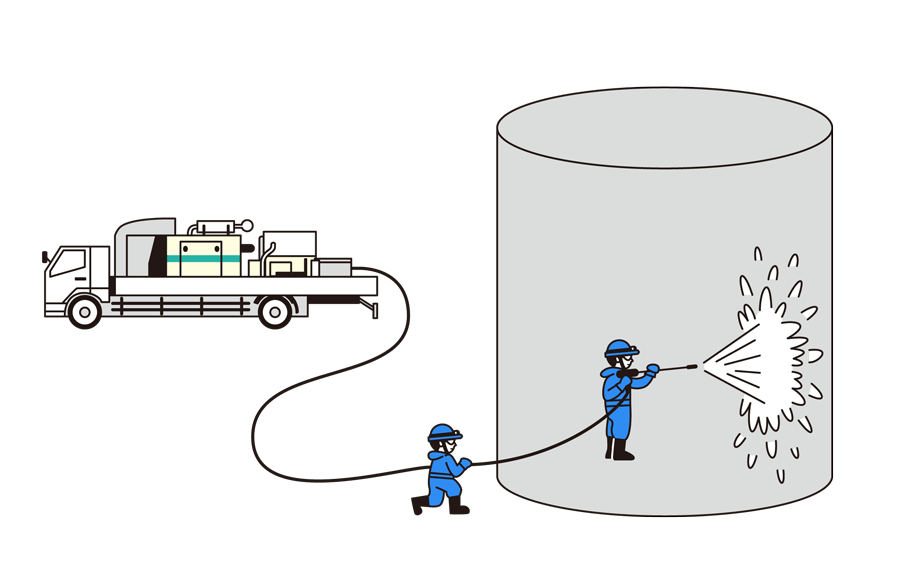
吸引作業後に高圧洗浄することで、より美しく仕上がります。汚れがなくなった分、貯蓄タンクなどの容量増加にもつながります。
水処理・汚泥処理
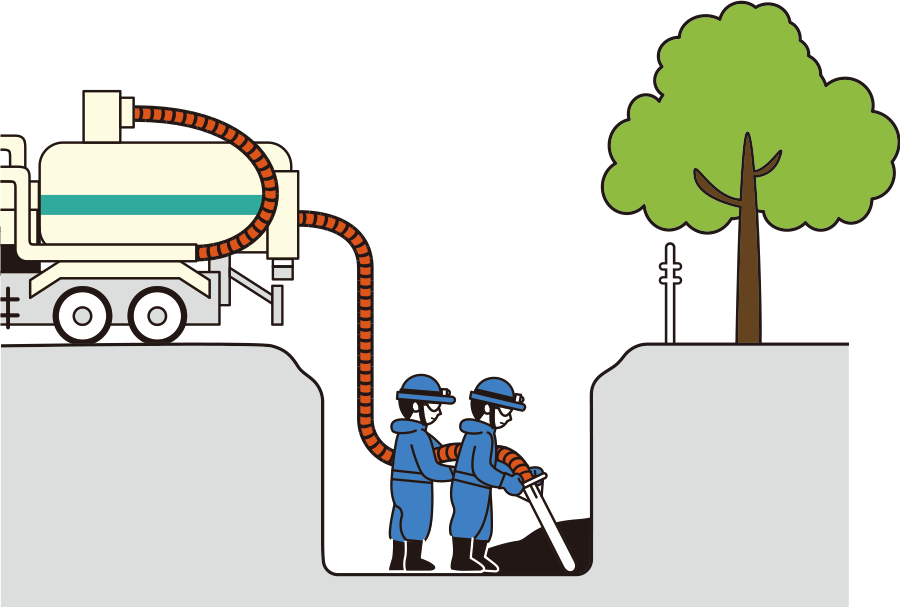
排水の処理がうまくいかない、汚泥の処理量が多く産廃費が高額といった問題点があればご相談下さい。専門のスタッフが代替案をご提案致します。
処理・設備トラブル対応
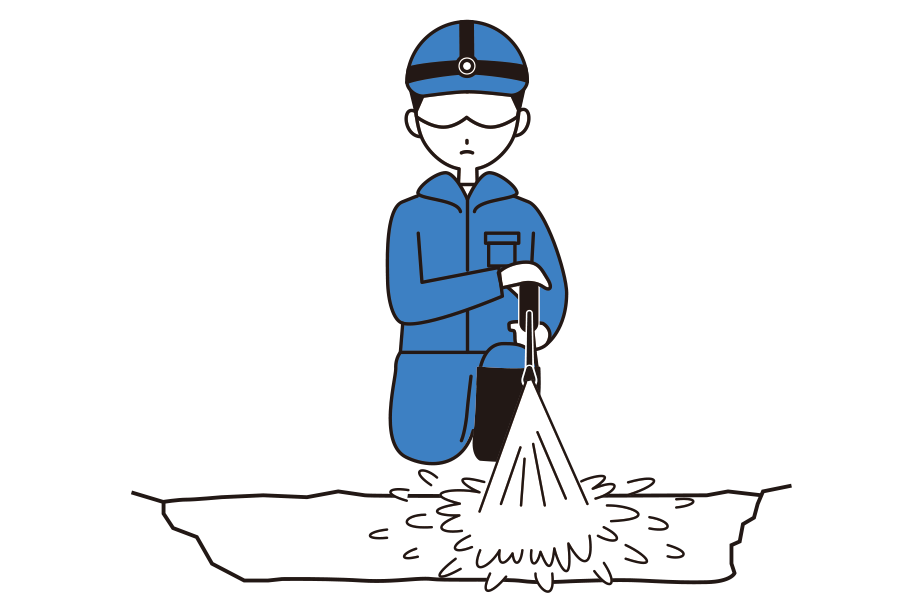
排水処理設備が止まった、工事現場から汚水が出てきた、タンクから油が流出したなどトラブル対応致します。まずはご連絡下さい。
吸引作業の省人化(人間から、重機が吸引する時代へ)
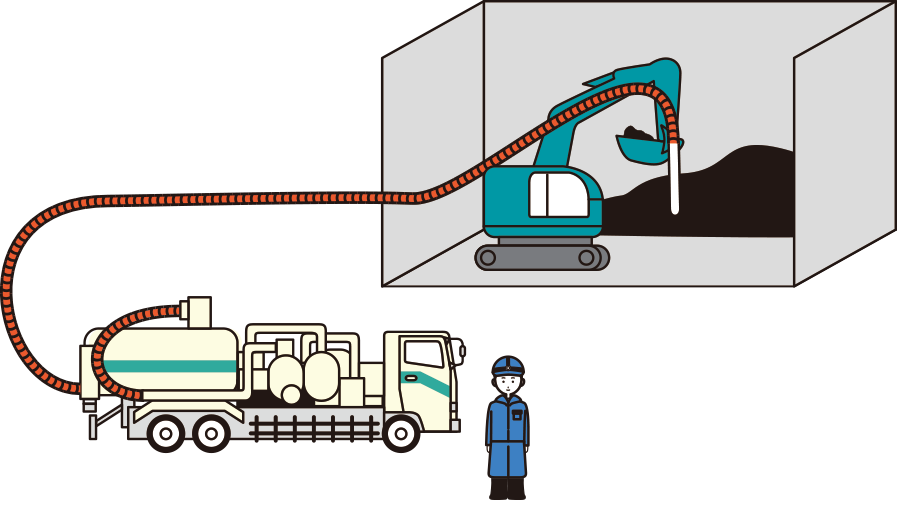
ピット内の通気性の悪さ、熱中症の危険リスク、ホースの暴れによる接触リスクなどの3Kの作業環境を作業方法の進化で環境改善を図ります。また、新型アタッチメントの開発で、特許取得を目指しています。